«Time is money»
Needless to say, it is a very true sentence, especially in the shipping industry.
As we consider the customer’s benefit as a top priority, we try to find the most cost-saving solutions from the beginning to the end of a project. Furthermore, with the accumulated experiences of BWTS retrofitting, we have provided advice about what to be prepared before starting the installation and how to do it in accordance with its plans.
Now, we would like to bring a project completed BWTS installation in 3.5 days.
Since a well-organized plan makes shortening retrofitting construction time, we made a detailed list indicating items that need attention.
The total quantity to be installed was 4,000kg of steel and 1,800m of electric cables. For the first day, we requested a widening hatch width by only 1cm. Even though it looks ignorable, however by doing so, we were able to avoid several times of trial-adjusting and all equipment was transported its installation position in two hours.
Only 10 people (6 men for steel, 4 men for electric) worked for installing a BWTS on this cargo vessel. The key points we could complete retrofitting in 3.5 days were first, there was no error on engineering drawings and minimized site-install pieces. Secondly, we didn’t miss anything even it’s so detailed. Finally, we shared all plans with everyone involved in the installation clearly so that every party knows what they should do.
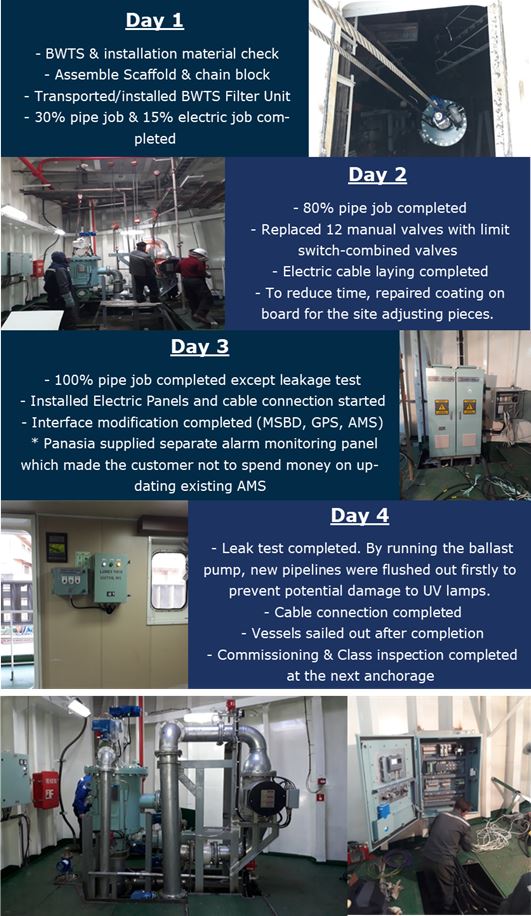
Well-being managed project in much adversity
There are lots of subjects to bother the planned schedule on retrofitting BWTS in this market, but regardless of what keeps making us hard, we are standing well. One of the on-going projects to provide our qualified system to adopt New G8 certificate has been well-installed under the big supports from local partners.
From the starting point to negotiate this project contract, the customer had a tight cost limit on its retrofit project. So, they diversified the parties in charge of each session, manufacturing the system from Panasia, retrofit engineering from a local company which had experienced some actual reference list in a retrofit project, but offered at the lowest level to the customer.
As the turnkey solution provider in retrofitting BWTS & Scrubber, only one way to get this project progress smooth was that Panasia should provide all useful know-how in the retrofit process. Also, because of re-scheduling installation, the system had to be compliant with the New G8 certificate which has been new criteria for the system installation on or after Oct. 28th. 2020. In this matter, we needed to re-submit the final system drawing to the registered class for the additional approval and the other one to make us bothered again was the vessel was registered of which we had not got the flag approval.
So, two times, two certificates had to be issued and managed at the same time. At this point, you must be so curious about the result. If we couldn’t make it, I wouldn’t write this article, we made all regulatory requirements successfully based on consistent communication amongst all parties involved in this project. Even now, we are figuring out to speed up the commissioning process in favor of relieved-restriction on entering the country where to be arranged of its commissioning. Each party has been hard to cooperate in the listed work below.
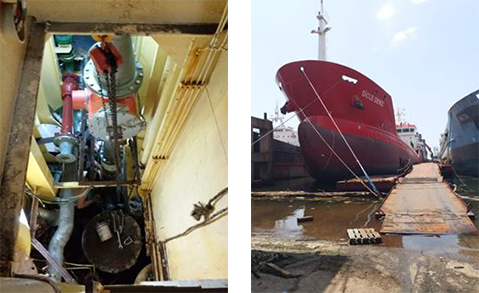
Owner
– Arranging the reliable shipyard before receiving the system in advance
– Calling for each engineer from each system to integrate the main signal with BWTS
– Gathering all parties to arrange regular meetings to revert on the fixed schedule
Shipyard
– Ready of analyzing installation manual in advance
– Reverting on the available man-power caused by COVID 19 in response to the planned installation schedule
Engineering company
– Basic & Detailed engineering including making all retrofit drawings
– 3D scanning job
– The matchmaker between the Owner and Maker in technical parts of the retrofit discussion
Maker
– Manufacturing the qualified system in compliance with USCG / IMO standard
– Receiving all required certificate and approval to fit this project
– Timely shipping schedule for the system
– Scheduling commissioning
– Local quarantine status quo
Currently, we have seen some project delays triggered by COVID 19 issues and we could summarize some cases 1) Many shipyards have been undermanned for preparation and management of the dry-docking of vessels. 2) Engineering companies would not be ready of starting engineering jobs due to travel restrictions in some parts of the world. 3) Makers would not be ready to receive a New G8 certificate due to the postponement of the regular MEPC meeting. Please be surely reminded that we could bring the experience on the successful project results no matter what.

Every single unhappy issue around the BWMS market has made all players bothered in compliance with the regulation. Furthermore, Ive heard the following bad news that one of the experienced suppliers adapted to UV technology decided to wind down their BWTS business in the market due to the huge competition with many players and regulatory uncertainty dragged for a long time.
Back in the beginning of opening BWTS market around 2010, there were more than 70 suppliers adapted to various treatment technologies, but all single players were pretty much sure that the market shall be one of the most promising because of the universal mandatory regulation compliance, but it’s far from being the initial expectation.
Due to lots of uncertainties related to the regulation, many suppliers like the dropouts who decided to go out of this business sector stated being less confident in holding up their cash-flow till the regulation comes up. The more serious thing was even one of USCG approved-maker handed over their business to the others not specialized in the BWTS market.
As of now, The numbers of systems approved by USCG are total 32 and the New G8 certified systems are 16. All of the customers not yet making a selection for the maker would be under an unconvincing position because none of the makers confess their long-term business plan in the negotiating phase with the customers.
Back to the point of the regulation timeline, no one could deny that the point is the regulations under the regime of IMO & USCG related to BWTS have been effective respectively regardless of these unfavorable issues. Getting through the de-coupling phase between dry-docking schedules and IOPP certificate renewal date in Sep. 2017, each of vessels has a firm schedule to install the system as of present if there’s no inevitable reason to delay it.
So, we could easily expect there will be a certain period to have many system installation schedules. To consider the latest news one of supplier is out of this market, it’s time for all owner or operator to think much of the availability of the experienced supplier in BWTS market because there’re only a few reliable makers survived in this market and each of them has their specific capability to manufacture their system in light of their regular process with all required certificate, approval.
Of course, many of factors shall be taken into consideration unexpected things could be popped up all of sudden like COVID 19, but through this article as all of the decision process including making a contract with a supplier, shipyard, engineering company gets through, I stressed the system maker’s endurance to maintain their business even when bumping into unexpected variable issues for your wise maker evaluation. It would be much more relaxing if you could be with the financially, technically reliable makers capable of providing generous experience accumulated for a long time. It’s the first step to maintain well-planning on a retrofit project, overcoming such challenges as may happen.

Back in the early stage of the BWTS industry, there was a debate of using a filter in the Ballast Water Treatment System because some clients complained about potential filter clogging during the operating. Nowadays, you can’t find the BWTS without the filter as a preliminary treatment method to remove large organisms however, the possibility of filter clogging remains still.
You can agree that using the filter will increase the potential risk to suspend the BWTS operation at the area where the quality of the water is severe but ironically, at the same time, without the filter, you can’t achieve more stringent standard at the end. It would be easy for you to just checking out what certificates BWTS vendors have but to look into deep, more to look at while ensuring the safe and reliable use or operate the BWTS.
1) Size of the Filter screen
Filter mesh size is a very critical element of the filter that it physically screen out the large organisms. As we have seen in the market, there are various sizes in filter mesh, we have seen a BWTS vendor using 20um minimum but commonly and widely 50umm is selected. To visualize the size, the pictures below ;
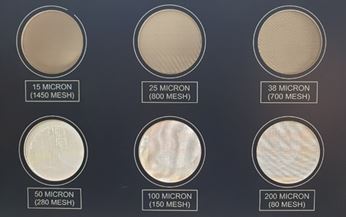
Even with your naked-eyes, the difference between 25 and 50 is easily noticeable. But you have to consider the fact that smaller size filter mesh maybe gives you better performance profile in testing scale but not always the case because chances to clog and bigger backpressure is also increased.
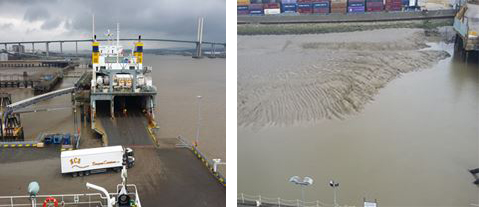
2) Filter Cleaning mechanism or program
You may face challenging water just like this or even worse. It is obvious the filter can easily clog with this kind of water shown. Advised that it is also important to check the water quality and depth around the vessel before the commencement of Ballast water operation or recall your previous experience in regions for any filter clogging. Usually, once the filter is clogged, it is complicating to make it re-operational so the recommendation is to prevent the filter clogged by lowering the DP value to activate the cleaning mechanism earlier than usual. Or some vendors provide the filter clogging solution in their control program to ease your operation. Also, you are advised to carefully evaluate the filter inlet pressure during the retrofit engineering phase. Higher location, pressure loss, degraded pump performance, and more will affect the efficiency of filter cleaning.
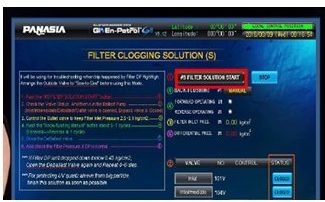
3) Recommendation
- Maintenance: it is recommended to clean the filter element after ballasting at the challenging condition to investigate any debris, mud, small particles, etc remained on the filter.
- Record keeping : Usually, every 5 months or less, crew changes are expected. It is a good practice if you record the water quality and BWTS operating profile during your port stay for your next reliever.
- BWTS vendors have an SW update or HW update especially for high turbidity water, so your vessel travels lots in those areas, you may contact vendors to find out more information about how to deal with high turbid water.